Cleaning verification dilemma of manufacturing equipment: Can the analytical method validation fail due to the cleanliness of the stainless steel surfaces?
In the pharmaceutical industry, the majority of the non-disposable equipment is made of electropolished, stainless steel material. The cleanliness of non-dedicated equipment should be verified before subsequent release for use in the manufacture of other intermediates, active pharmaceutical ingredients (APIs), or drug products to prevent cross-contamination. The cleaning procedures should be validated, including the analytical methods associated to the processes. Although the U.S. Food and Drug Administration (FDA) has raised awareness to the potential of cross-contamination, it still has issued numerous warning letters due to inadequate cleaning, failure to validate the cleaning verification method, and failure to follow cleaning procedures.
It is standard practice in industry that the validation of the analytical methods for cleaning verification be performed (mostly) on stainless steel coupons (e.g., 316L, 50 cm2) with the same surface/finish (e.g., roughness average, Ra 20) as the manufacturing equipment. During the development and validation of these analytical methods, the sample of interest is spiked at the target residue level onto the stainless coupon determined by the maximum allowable carry-over (MACO) limit and recovered by swabbing or wiping the surface of the coupon (Fig. 1).
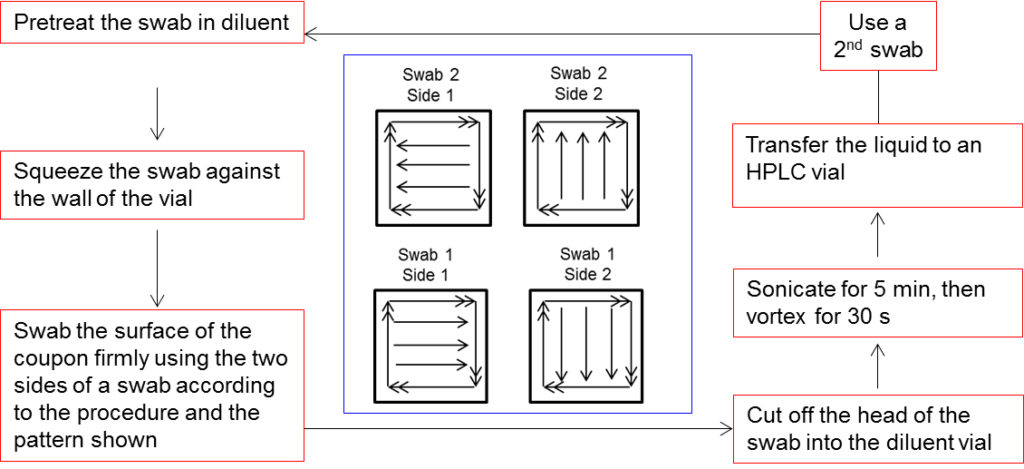
Fig. 1. Example of swabbing procedure during analytical method validation for cleaning verification of the manufacturing equipment.
分析方法的开发和验证or cleaning verification has always been challenging and problematic as it is a trace analysis technique. At trace levels, several sources may contribute to variability such as change in the sample composition, purity of reagents used, presence of microorganisms, matrix effect, adsorption, drug product degradation, evaporation of the components of interest, etc. Inconsistent recoveries of the residues from the coupon surfaces can range, as in our case, from excellent (97 ± 1%) to failing (50 ± 4%). The variability in results was observed at different spike levels, at various ratios of API/excipient, amongst different analysts, and even for the same analyst on different days.
The variability in the recovery results with the parameters studied above led to investigating whether the coupon surface was a source of variability. Simply preparing the coupon surface by rinsing and wiping with water and methanol did not improve recovery consistency. The approach was modified to include fully immersing and sonicating the coupons in CIP100 and CIP200 solutions, basic and acidic, respectively, commercial cleaning agents. By applying this cleaning procedure to previously used coupons that failed the recovery acceptance criteria, multiple analysts were able to obtain consistent recoveries from day-to-day for different APIs and API/excipient ratios at various spike levels. Figure 2 shows a consistent improvement in recovery from one trial to another, at different drug loads, and from the surfaces of four different coupons. The approach was successfully applied for cleaning verification of small molecules (<1000 Da) as well as large biomolecules (up to 50,000 Da).
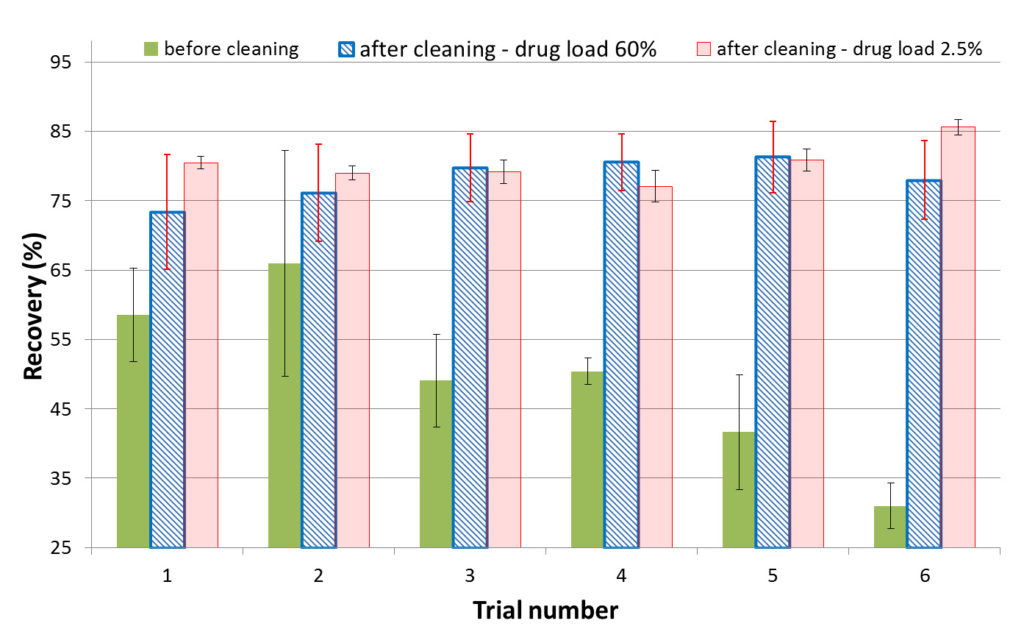
Fig. 2. Comparison of recovery of a small molecule API on four different coupons before and after cleaning at two different drug load levels.
The lack of a well-defined procedure and cleaning agents for cleaning the coupon surface was the major contributor to low and variable recoveries. The recovery problems may be due to deposition of residue material on the surface and/or a change in the oxidation state of the surface of the coupon (i.e., enthalpic interactions with the sample are introduced). The cleaning verification dilemma of analytical methods failure was traced to the lack of cleanliness of the stainless steel surfaces.
Andrei Blasko, Imad A. Haidar Ahmad, James Tam
Novartis Pharmaceuticals Corporation, San Carlos, CA, USA
Publication
Cleaning verification: Exploring the effect of the cleanliness of stainless steel surface on sample recovery.
Haidar Ahmad IA, Tam J, Li X, Duffield W, Tarara T, Blasko A
J Pharm Biomed Anal. 2017 Feb 5
Leave a Reply
You must belogged into post a comment.